Detailed Explanation of SMT Component Pin Coplanarity
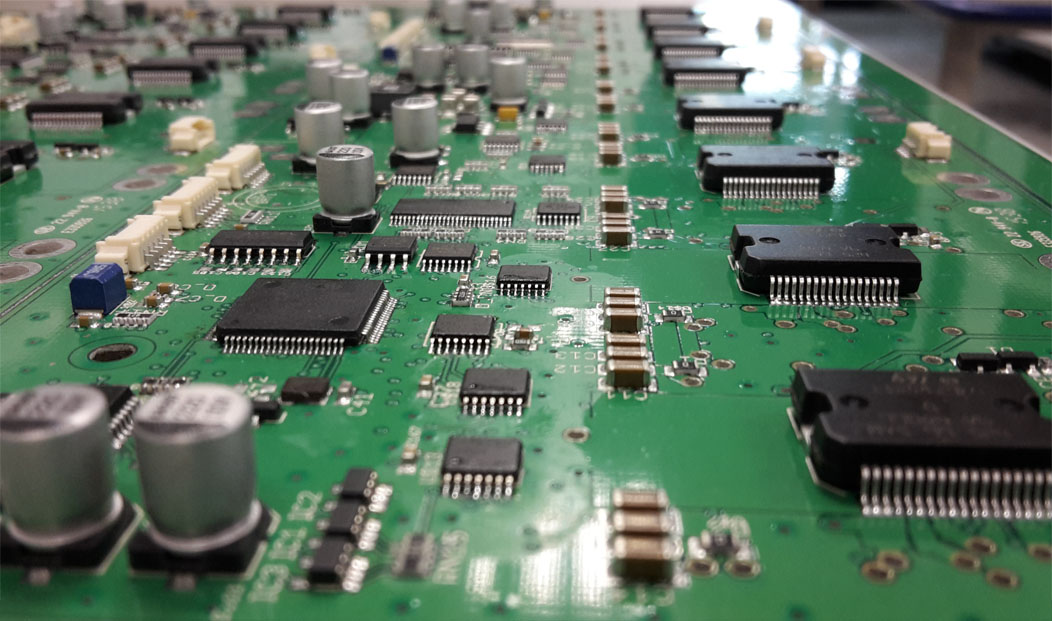
In the electronics manufacturing industry, the coplanarity of SMT (Surface Mount Technology) component pins is a critical concept. Coplanarity refers to the degree to which component pins lie in the same plane, playing a pivotal role in ensuring the reliability and efficiency of SMT assembly processes. This article provides a comprehensive analysis of SMT component pin coplanarity from various perspectives, optimized for Google SEO with relevant keywords and structured content.
Definition and Importance of Coplanarity
Coplanarity, or pin coplanarity, measures the deviation of SMT component pin ends from an ideal plane. Ideally, all pins should be perfectly coplanar to ensure optimal contact with PCB (Printed Circuit Board) solder pads during the SMT assembly process. Poor coplanarity can lead to soldering defects such as poor solder joints, cold soldering, or incomplete connections, ultimately compromising the performance and reliability of electronic products.
Factors Affecting Coplanarity
Several factors influence the coplanarity of SMT component pins:
- Component Packaging Process: The packaging process directly impacts pin coplanarity. Improper pin fixation or uneven heating during packaging can cause pin deformation, affecting coplanarity.
- Material Selection: The choice of pin materials significantly affects coplanarity. Some materials are prone to deformation under heat, leading to reduced coplanarity.
- Transportation and Storage: External forces such as pressure or impact during transportation and storage can deform pins, disrupting their coplanarity.
Detection and Improvement of Coplanarity
Detection Methods: To ensure the coplanarity of SMT component pins, accurate measurement techniques are essential. Common methods include:
- Optical Inspection: Uses visual systems to measure pin alignment.
- X-Ray Inspection: Detects internal pin deviations.
- 3D Scanning: Provides precise measurements of pin deviations from the ideal plane.
These methods provide reliable data for subsequent improvement efforts.
Improvement Measures: To address coplanarity issues, consider the following strategies:
- Optimize the component packaging process to ensure uniform heating and secure pin fixation.
- Select stable pin materials to minimize heat-induced deformation.
- Enhance protection during transportation and storage to prevent external damage to pins.
- For applications requiring high coplanarity, employ pin reshaping techniques to fine-tune pin alignment.
Impactof Coplanarity on SMT Assembly
The coplanarity of SMT component pins is crucial for the success of SMT assembly. Components with good coplanarity ensure proper contact between pins and PCB solder pads, improving soldering quality and production efficiency. Conversely, poor coplanarity can result in soldering defects, such as incomplete or weak solder joints, leading to rework, scrap, increased production costs, and delayed delivery.
Conclusion
The coplanarity of SMT component pins is a key factor in ensuring the reliability and efficiency of SMT assembly processes. To maintain optimal coplanarity, manufacturers must focus on improving packaging processes, selecting appropriate materials, and implementing robust transportation and storage practices. Additionally, employing advanced detection methods and improvement measures is essential. During SMT assembly, continuous monitoring of coplanarity and timely adjustments to process parameters and techniques are critical to achieving seamless production.