Flatness vs. Coplanarity: Key Differences and Measurement Methods Introduction
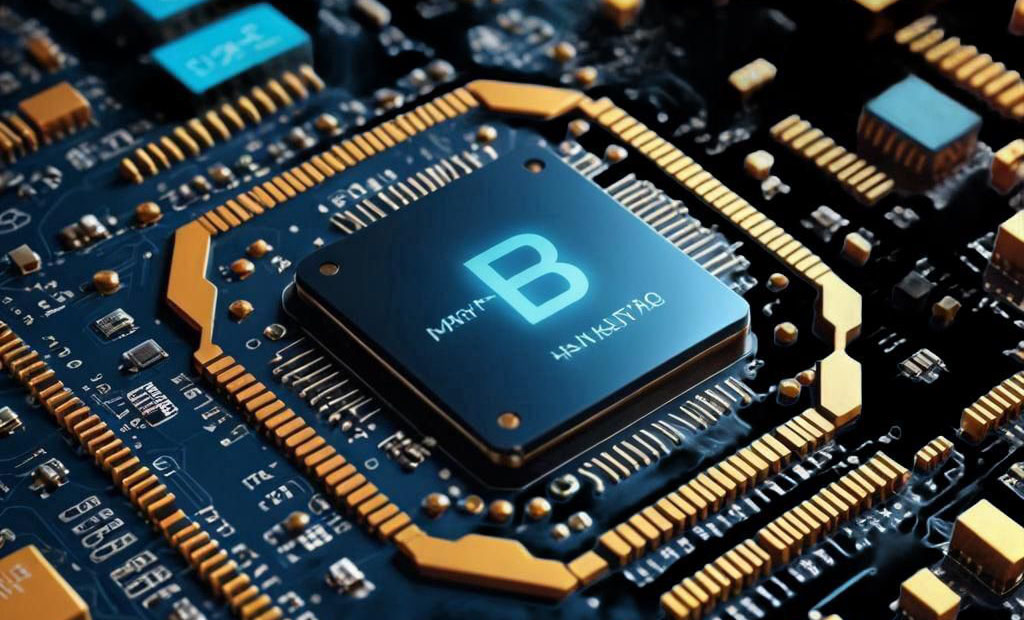
In precision manufacturing and quality control, flatness and coplanarity are critical surface measurement parameters. While both relate to geometric tolerances, they serve different purposes. This guide explains the key differences between flatness and coplanarity, their applications, and how they are measured in industries like PCB manufacturing, automotive, and aerospace.
1. What is Flatness?
Flatness measures how much a single surface deviates from a perfectly flat plane. It ensures that a surface is uniform without warping, bumps, or depressions.
Key Characteristics of Flatness
✔ Applies to a single surface (e.g., a tabletop, metal sheet, or PCB substrate).
✔ Measured using optical profilometers, laser scanners, or CMMs (Coordinate Measuring Machines).
✔ Tolerance is defined as the maximum allowable deviation from an ideal flat plane.
Applications of Flatness Measurement
Machined parts (ensuring smooth contact surfaces).
Semiconductor wafers (preventing warping in chip production).
Glass panels (avoiding distortions in displays).
2. What is Coplanarity?
Coplanarity measures whether multiple surfaces or points lie on the same flat plane. It ensures alignment across different components, such as PCB solder joints or mechanical assemblies.
Key Characteristics of Coplanarity
✔ Applies to multiple surfaces or points (e.g., IC pins, connector leads, or mounting pads).
✔ Measured using 3D optical inspection systems or specialized coplanarity testers.
✔ Critical in electronics manufacturing to prevent soldering defects.
Applications of Coplanarity Measurement
PCB assembly (ensuring all solder balls in a BGA package are at the same height).
Automotive components (checking gasket alignment).
Aerospace structures (verifying panel flushness).
3. Key Differences Between Flatness and Coplanarity
Feature Flatness Coplanarity
Definition Measures deviation of a single surface from a perfect plane. Measures alignment of multiple surfaces/points on the same plane.
Measurement Scope Single-plane inspection. Multi-point or multi-surface inspection.
Tools Used Laser scanners, CMMs, optical flats. 3D optical testers, coplanarity gauges.
Industry Use Cases Machining, glass manufacturing, semiconductor wafers. PCB assembly, automotive gaskets, aerospace panels.
Tolerance Impact Affects surface uniformity. Affects component fit and soldering reliability.
4. How to Measure Flatness and Coplanarity
A. Measuring Flatness
Contact Methods (e.g., dial indicators, surface plates).
Non-Contact Methods (e.g., laser interferometry, white light scanners).
B. Measuring Coplanarity
Optical Inspection Systems (e.g., automated vision systems for PCB inspection).
3D Profilometers (for high-precision component alignment checks).
Best Practice:
For flatness, use high-resolution laser scanning for micron-level accuracy.
For coplanarity, automated optical inspection (AOI) is ideal for fast, repeatable measurements.
5. Why Are These Measurements Important?
Flatness errors → Cause leaks, poor sealing, or uneven wear in mechanical parts.
Coplanarity errors → Lead to soldering defects, electrical failures, or misassemblies in PCBs and connectors.
Example: In BGA (Ball Grid Array) packages, poor coplanarity can result in cold solder joints, leading to device malfunction.
6. Conclusion: Choosing the Right Measurement Method
Understanding the difference between flatness and coplanarity helps manufacturers:
✔ Improve product reliability by ensuring proper surface alignment.
✔ Reduce defects in PCB assembly and precision engineering.
✔ Select the right inspection tools (e.g., laser scanners for flatness, AOI for coplanarity).
For high-accuracy inspections, combine 3D metrology and automated vision systems to ensure both flatness and coplanarity meet industry standards.