Applications of Coplanarity Testing Across Industries
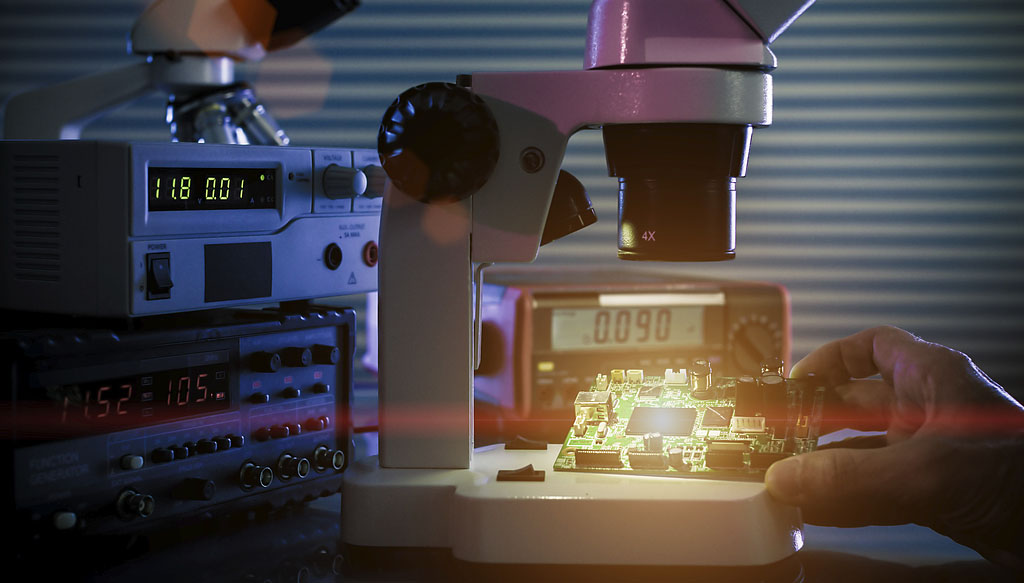
“Coplanarity testing“ measures whether multiple points, lines, or surfaces lie on the same geometric plane, ensuring precision in manufacturing and assembly. Unlike flatness testing (which checks a single surface), coplanarity focuses on the alignment of multiple independent elements. Below are its key applications across industries, optimized for technical accuracy and SEO relevance.
————————————————————————————————————————–
1. Electronics Manufacturing
– PCB Assembly (SMT Process): Ensures coplanarity of solder balls in ”BGA (Ball Grid Array)“and ”QFN (Quad Flat No-leads)“ packages for reliable soldering.
– Connector/Socket Inspection: Verifies pin or contact coplanarity to prevent poor electrical connections.
– Flexible PCBs (FPC): Maintains layer alignment in multilayer flexible circuits to avoid signal interference.
2. Semiconductor & Packaging
– Chip Packaging: Tests”wafer bonding” and”flip-chip” coplanarity to improve yield and thermal performance.
– Probe Cards: Ensures uniform probe tip alignment for accurate wafer testing.
3. Automotive & Aerospace
– Engine Blocks & Cylinder Heads: Checks sealing surface coplanarity to prevent oil or gas leaks.
– Turbine Blade Mounting: Ensures uniform base alignment for optimal aerodynamics.
– Car Body Welding: Verifies panel coplanarity for structural integrity and aesthetics.
4. Precision Machinery & Automation
– Robotic End Effectors: Maintains gripper coplanarity for stable object handling.
– CNC Machine Tables: Ensures T-slot or fixture alignment for machining accuracy.
– 3D Printing Beds: Calibrates multi-nozzle or laser coplanarity for consistent layer deposition.
5. Optics & Display Technology
– AR/VR Lens Modules: Aligns multiple lenses for sharp imaging.
– LCD/OLED Panels: Checks backlight and display layer coplanarity to prevent brightness unevenness (Mura effect).
6. Medical & Bioengineering
– Artificial Joints (Knees/Hips): Ensures implant contact surface alignment for durability.
– Microfluidic Chips: Maintains channel coplanarity for precise fluid control.
————————————————————————————————————————–
Coplanarity Testing Methods
– Optical Measurement (Laser coplanarity testers, 3D scanners)
– Contact Measurement(Dial indicators, height gauges)
– Machine Vision(AOI – Automated Optical Inspection)
Why Coplanarity Matters for Quality Control
Coplanarity testing is critical in high-precision manufacturing, electronics assembly, and automotive engineering, directly impacting product performance, reliability, and production yield.