Why Coplanarity Testing is Essential in LED Manufacturing?
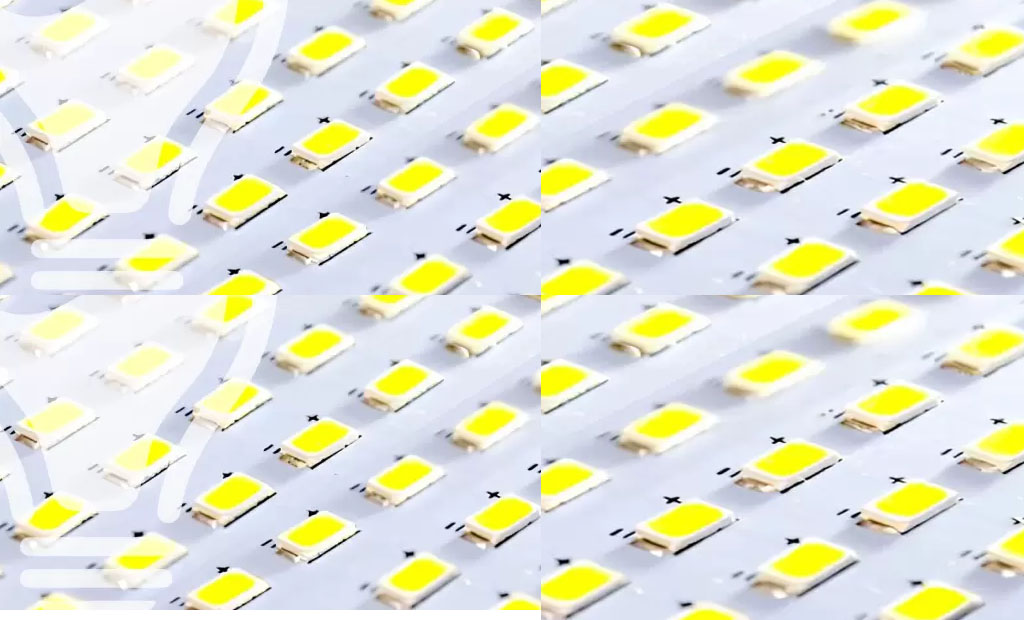
Coplanarity testing is a critical quality control step in LED production, ensuring product reliability and performance. Its necessity spans six key dimensions:
1. Ensuring Solder Joint Reliability
-
When pin coplanarity exceeds 0.05mm, reflow soldering issues arise:
• Non-wet opens (air gaps cause uneven heat conduction)
• Cold solder joints (reduced bond strength by 40-60%)
• 3-5x higher risk of weak solder joints (critical for automotive lighting)
2. Maintaining Optical Performance
-
Impact of coplanarity deviation on light output:
Deviation Luminance Uniformity Loss Chromaticity Shift (Δuv) 0.03mm 8-12% 0.002 0.10mm 25-30% 0.008 (Data from COB packaging tests)
3. Thermal Management Requirements
-
Real-world failure cases:
• 15°C increase in LED junction temperature due to poor coplanarity
• 2.3x faster lumen depreciation from increased thermal resistance
• Lifespan drops from 50,000 hrs to 18,000 hrs
4. Compatibility with Automated Assembly
-
Modern pick-and-place machine requirements:
• 0402 packages: ≤0.02mm tolerance
• Mini LEDs: ≤0.01mm (for mass transfer processes)
• Defective placement rate jumps from 99.99% to 97.5% if standards are exceeded
5. Cost Efficiency & ROI
-
Economic benefits of coplanarity testing:
(Based on real industry case studies)
6. Compliance with Industry Standards
-
Key certifications requiring coplanarity testing:
-
AEC-Q102: Automotive LEDs must maintain ≤0.03mm after 10-year aging
-
ENERGY STAR: Lumen maintenance requires ≤0.04mm deviation
-
IEC 62031: Mandates pin flatness inspection for safety
-
Emerging Trends in Coplanarity Testing
-
Miniaturization demands higher precision:
• Standard LEDs: 100μm-level testing
• Mini LEDs: 10μm-level requirements
• Micro LEDs: Moving toward 1μm-level accuracy -
Faster inline inspection: Speeds now reach 2000UPH (for large panel backlight production)
Leading Solutions Today
✓ 0.6μm accuracy at 800UPH
✓ AI-powered real-time correction
✓ Testing cost < $0.0007 per LED