Principle of Coplanarity Tester
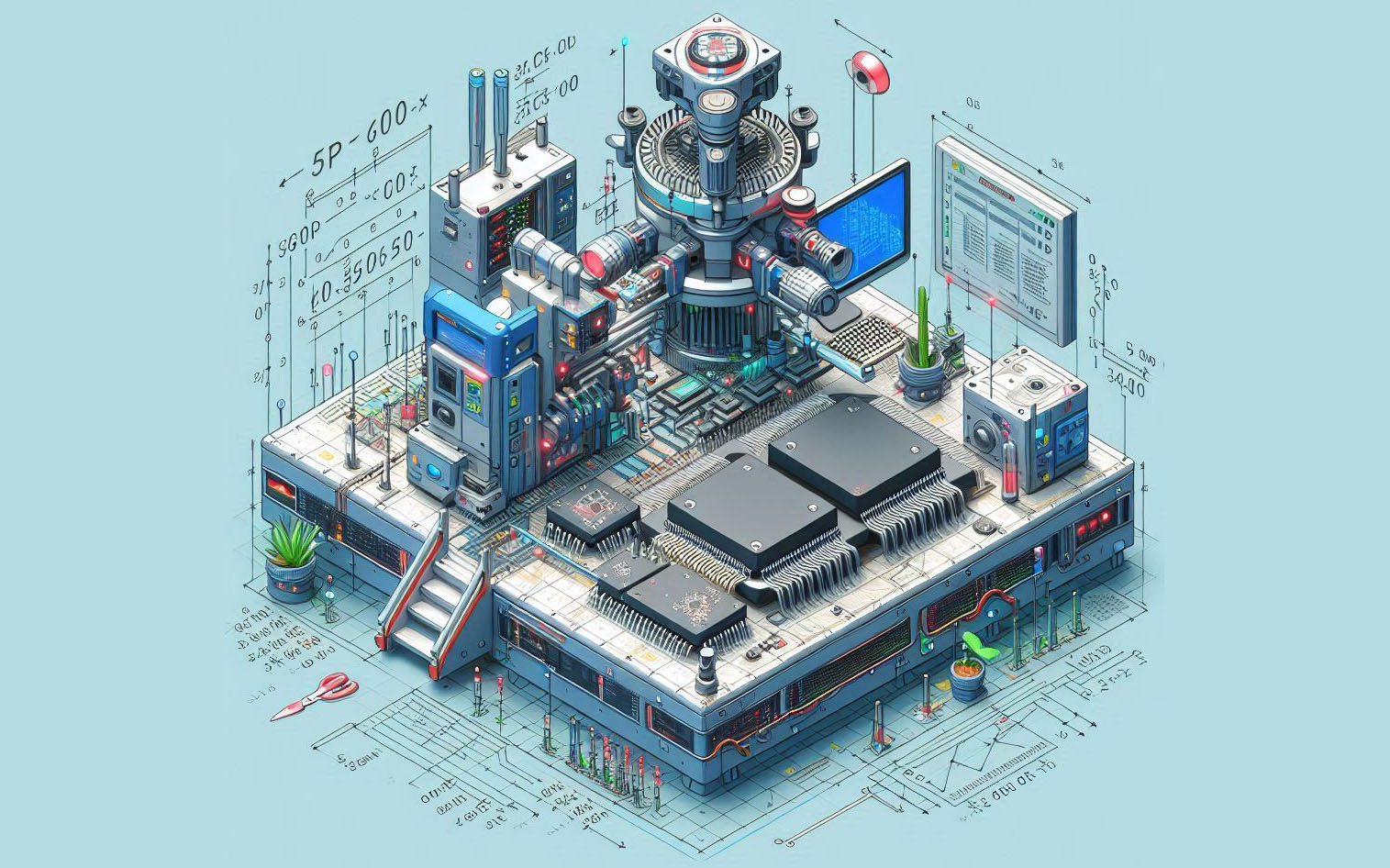
Coplanarity Detector: How It Works, Key Components & Applications Introduction to Coplanarity Detection
A coplanarity detector is an essential tool in industrial manufacturing and quality control, ensuring the flatness and precision of surfaces. This guide explores its optical measurement principles, lighting systems, and advanced image processing algorithms, helping you understand how it improves production accuracy and efficiency.
1. Optical Measurement Principle of Coplanarity Detectors
The optical measurement system in a coplanarity detector works by:
Illuminating the target surface with a bottom light source.
Capturing reflected light through a high-resolution lens and camera system.
Detecting deviations (protrusions, depressions, or bends) by analyzing changes in light reflection.
When a surface is not perfectly flat, the light deflects differently, allowing the system to calculate flatness errors with high precision.
Why It Matters:
✔ Ensures consistent product quality in industries like PCB manufacturing, automotive, and aerospace.
✔ Reduces human error compared to manual inspection.
2. Lighting System: Enhancing Detection Accuracy
The LED lighting system is crucial for high-accuracy coplanarity detection. Key features include:
Configurable Lighting Options
Multiple LED arrangements (ring, backlight, coaxial) for different surface types.
Adjustable brightness to highlight defects like scratches, warping, or uneven surfaces.
Benefits of Advanced Lighting
✔ Improves defect recognition for better measurement reliability.
✔ Reduces glare and shadows, minimizing false readings.
✔ Speeds up inspection time, boosting production efficiency.
Best Practice: Choose the right lighting setup based on material type (metallic, plastic, etc.) for optimal results.
3. Image Processing Algorithms: The Core of Detection
The image processing system determines the detector’s accuracy. Two main approaches are used:
A. Image-Based Processing
Uses grayscale analysis and phosphorescence techniques to detect surface irregularities.
Ideal for 2D flatness inspection (e.g., semiconductor wafers, PCB boards).
B. Point Cloud Processing (3D Scanning)
Converts images into 3D point cloud data for high-precision depth analysis.
Best for complex surfaces (e.g., automotive parts, molded components).
Which One to Choose?
For fast 2D checks → Image-based processing.
For detailed 3D analysis → Point cloud processing.